In Australia’s fast-evolving construction industry, builders are increasingly turning to light gauge steel framing over traditional timber — and for good reason. From durability and efficiency to sustainability, steel is proving to be a smarter, more reliable solution across residential and commercial builds alike. So why the shift? Let’s break it down.
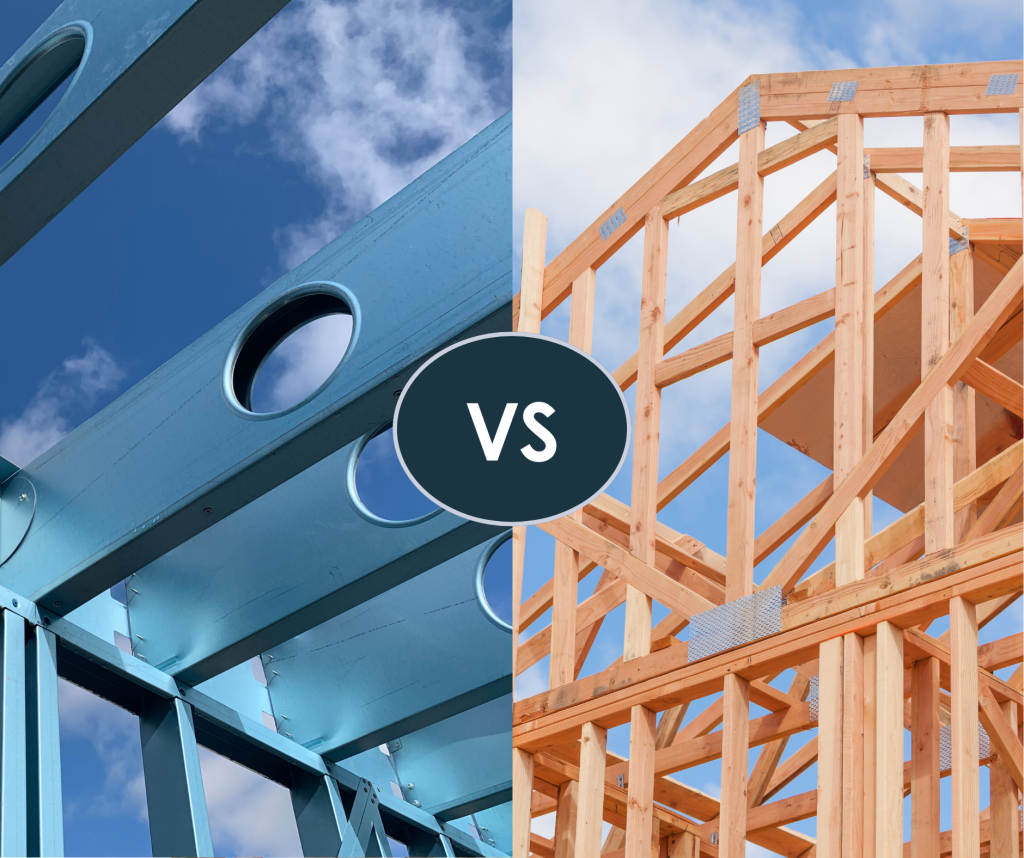
Durability That Stands the Test of Time
Timber may be tried and true, but steel is engineered for strength. Light gauge steel frames are termite-proof, non-combustible, and won’t rot, warp, or shrink — issues that can compromise the integrity of timber structures over time.
Whether it’s exposure to moisture, pests, or the elements, TRUECORE® steel frames manufactured by Dynamic Steel Frame maintain their structural integrity long after timber starts to degrade. That means fewer maintenance concerns and greater peace of mind for homeowners and developers alike.
Efficiency in Every Stage
Steel framing is designed with precision in mind. With advanced 3D modelling and BIM technology, frames are manufactured off-site and delivered ready to install. No guesswork. Just clean, efficient assembly.
For builders, this means:
- Faster installation timelines
- Reduced on-site labour and waste
- Fewer delays due to weather or material inconsistencies
At Dynamic Steel Frame, our system allows projects to move from concept to completion faster, saving time and money at every stage of the build.
Sustainability That Builds a Better Future
Sustainability is more than a trend — it’s a necessity. Steel is one of the most recyclable materials on the planet, with minimal waste and high recovery rates. Unlike timber, which relies on logging and treatment processes, steel production continues to evolve with cleaner, more sustainable methods.
By choosing light gauge steel, builders can lower their environmental impact without compromising on quality or performance.
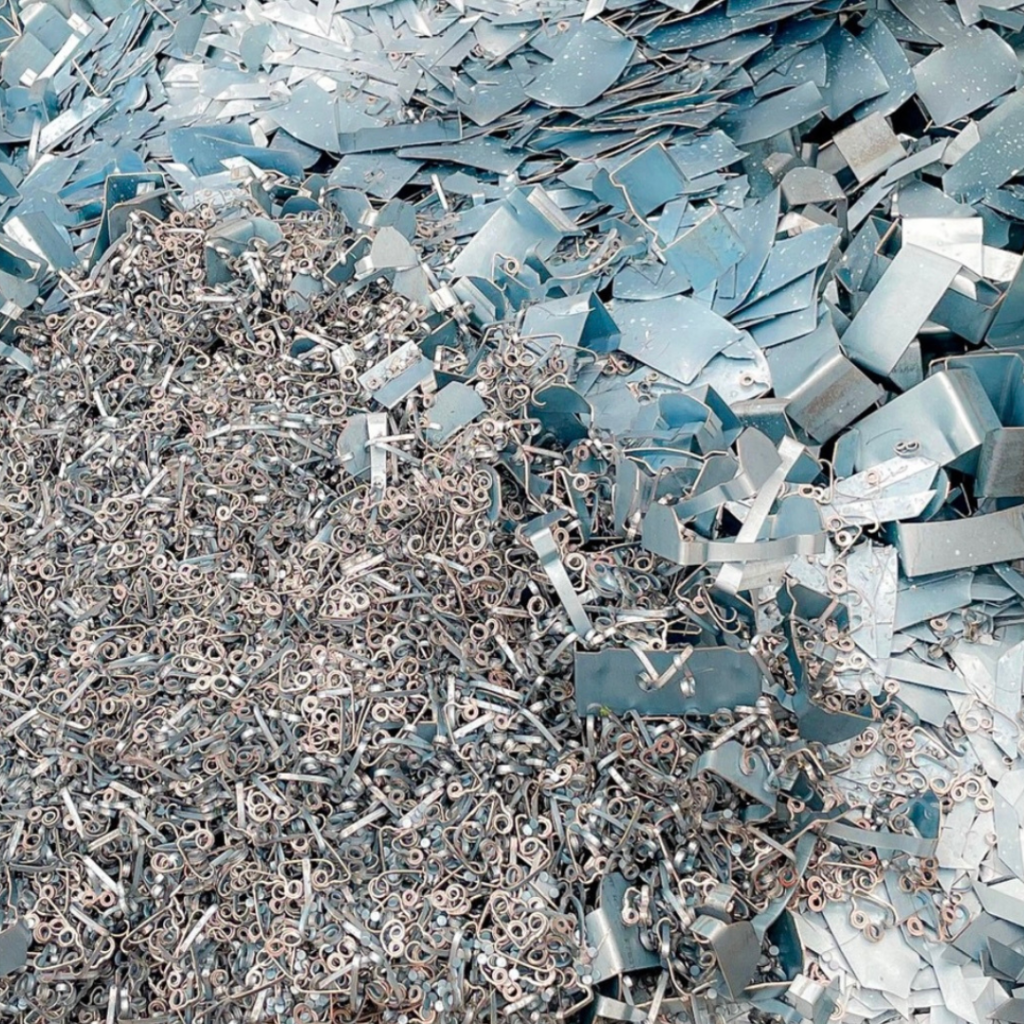
So, Why Are More Builders Making the Switch?
Simple — because steel delivers where timber can’t. Builders, architects, and developers are realising the long-term value of:
✅ Greater design flexibility
✅ Reliable strength and safety
✅ Faster build times
✅ Lower maintenance
✅ A smaller environmental footprint
Whether you’re planning a single home or a multi-storey development, light gauge steel offers a modern alternative that meets the demands of today’s construction industry.
Ready to build smarter?
Get in touch with the team at Dynamic Steel Frame to learn how our steel solutions can help bring your next project to life.
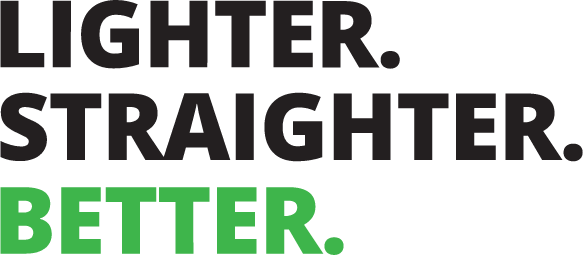
Phone: 03 9701 7342
Email: sales@dynamicsteelframe.com.au