Where we started to where we are now.
Dynamic Steel Frame is Victoria’s leading independent light gauge steel framing manufacturer and recognised globally as a leader in the field.
DSF began when director Peter Blythe identified a gap in the market for light gauge steel. There was demand for product but a distinct lack in production capacity. Starting with one man and a machine, growing over the years, to where we are today.
We manufacture for all segments of the building industry including commercial, residential, medium density, modular, social housing, bespoke homes, façades, and even tiny houses. Builders appreciate the BIM / Digital Twin approach to design enabling the designs to be ironed out before manufacture, resulting in reduced rework on site, fewer trades and faster erection times.
Combining design and engineering software with an automated rollformer to produce wall frames, roof trusses, floor joists and panels quickly and accurately. With our extensive experience and unmatched knowledge base we offer innovative solutions to your challenges.
The team at Dynamic Steel Frame pride themselves on impeccable, robust and fully compliant designs, customer service and industry knowledge.
Creating complex award-winning designs using innovative, cutting-edge technologies, the company has driven industry development and played a major role in the evolution of consumer embracement of using light gauge steel in the building process. Proudly Australian owned, supplied and manufactured, Dynamic Steel Frame is providing a Lighter. Straighter. Better. way to build.
If you can imagine it, we can build it.
DSF’s Operations
We currently operate the following machines and steel gauges:
Machines Operating
- 4 x 89mm
- 3 x 75mm
- 1 x 140mm
- 1 x 200-350mm
Steel Gauges
- 0.75 -1.6mm
- 1.2 – 2.4mm
Our production team has worked on various sized jobs, from tiny homes to large scale townhouse developments and facade’s.
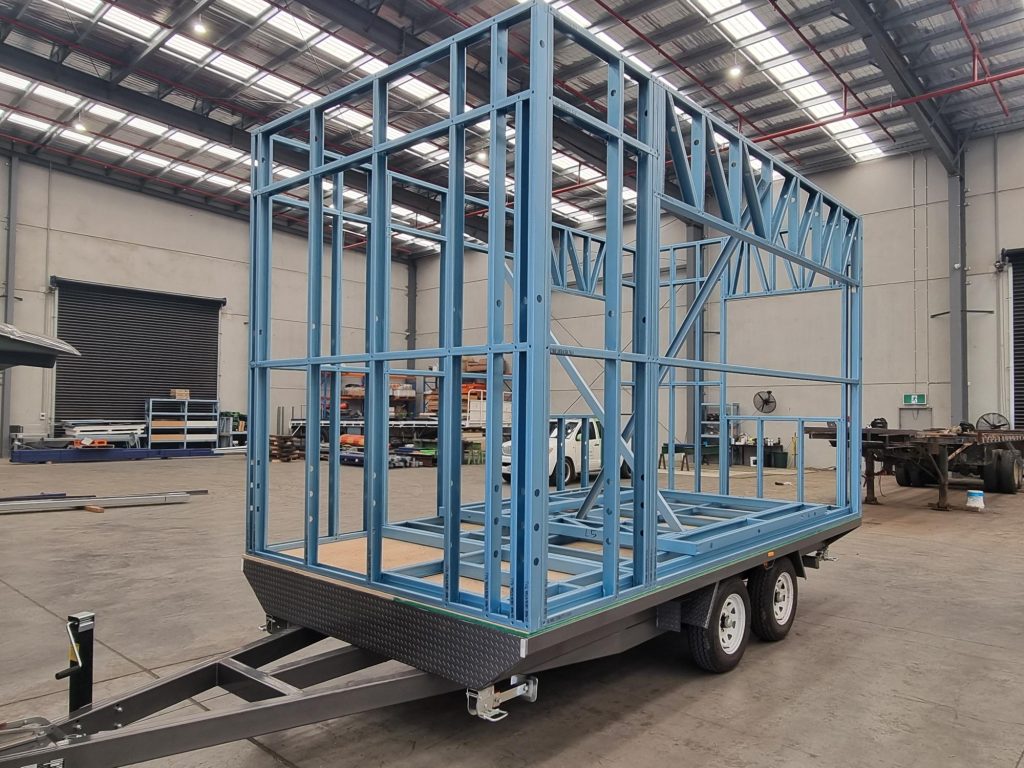

Dynamic Steel Frame was apart of a ground breaking project, producing 18 light gauge steel modules each spanning 8m wide & 15m high and requiring over 3 tonne of Truecore steel. Contain the worlds largest light gauge steel facade modules, this project went on to win the Victorian Steel Excellence Award for steel clad structures in 2020.
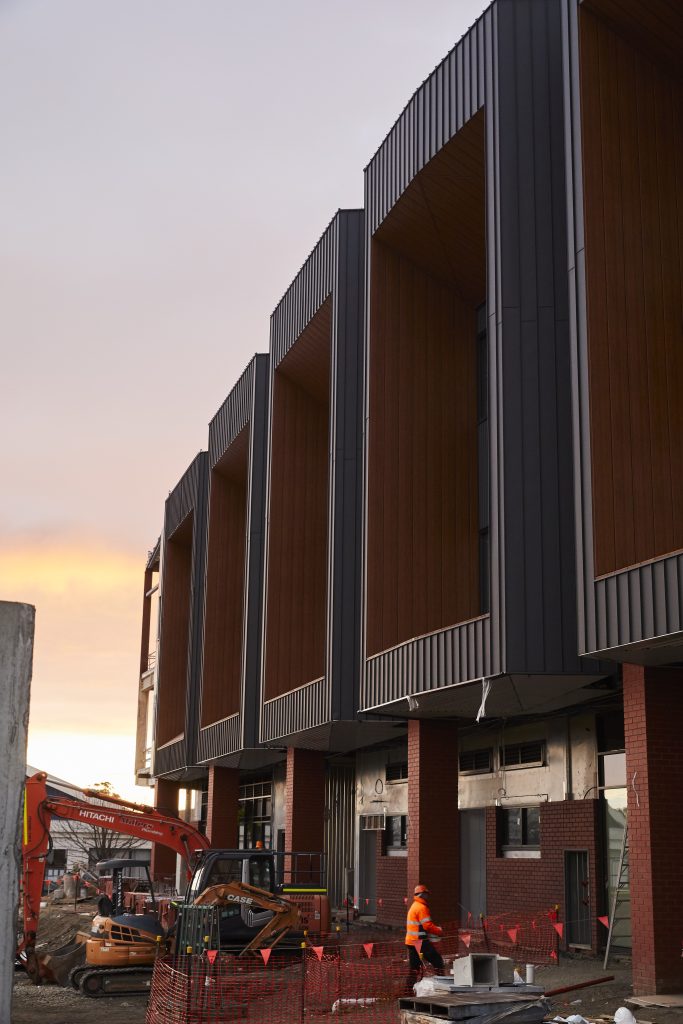
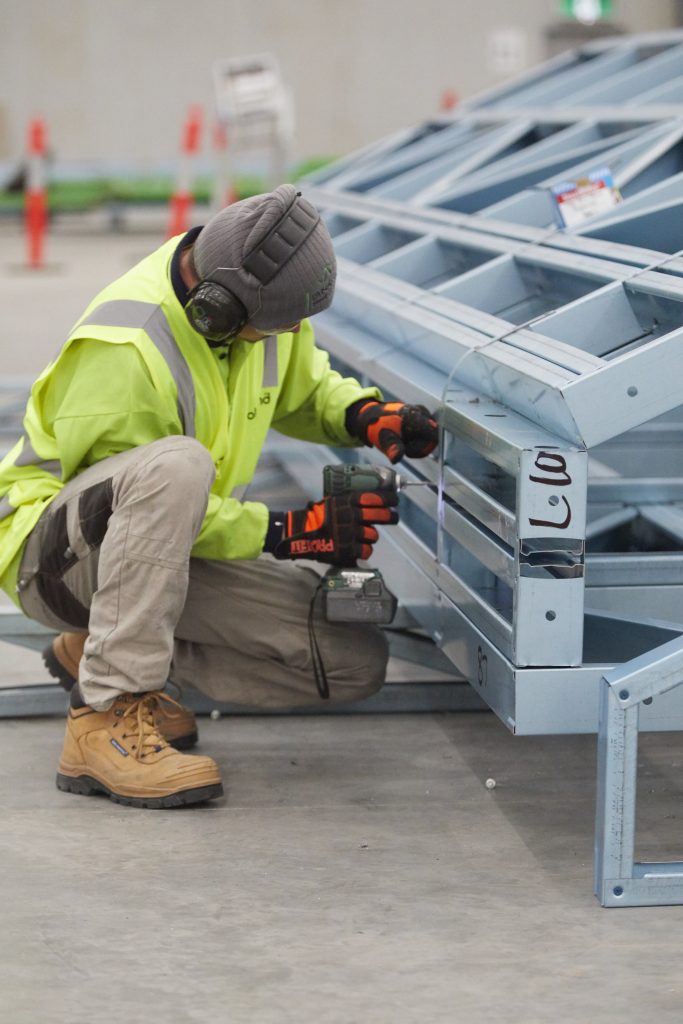
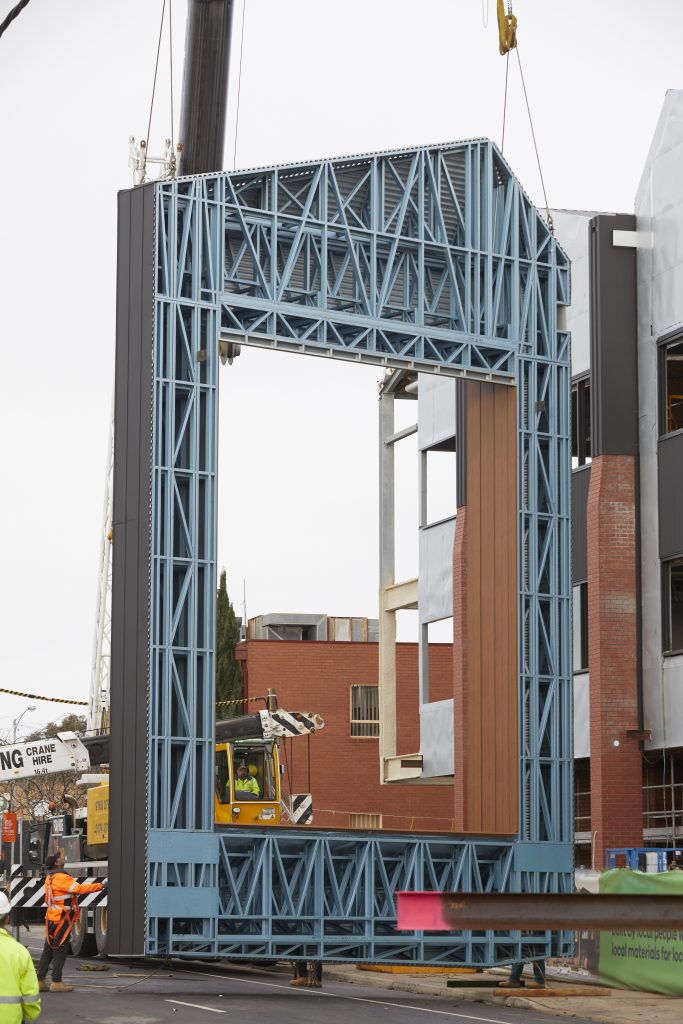
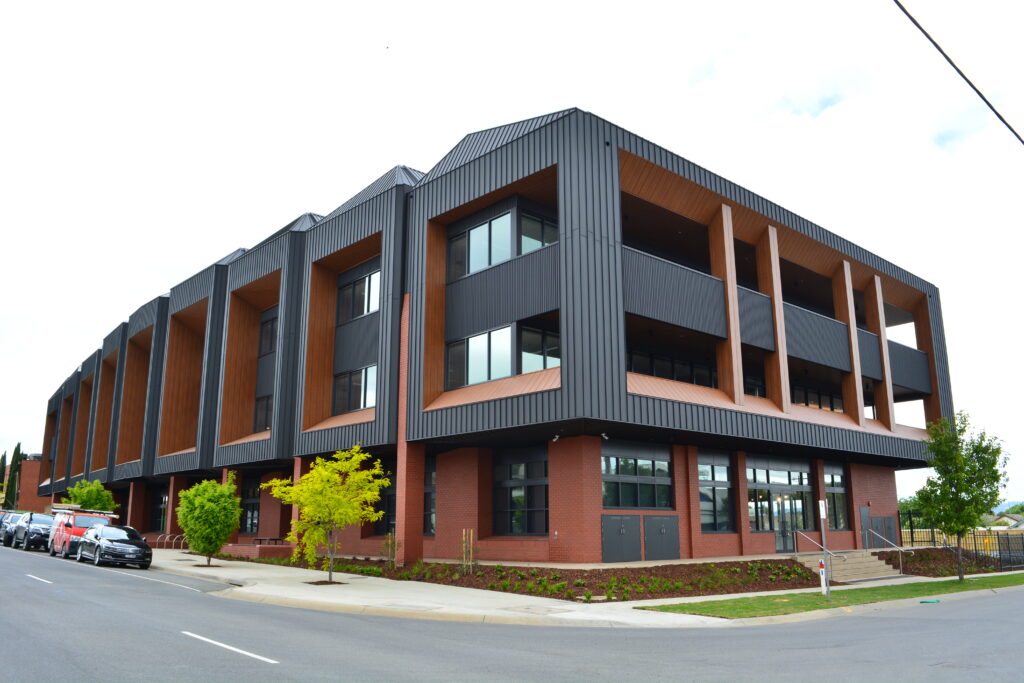
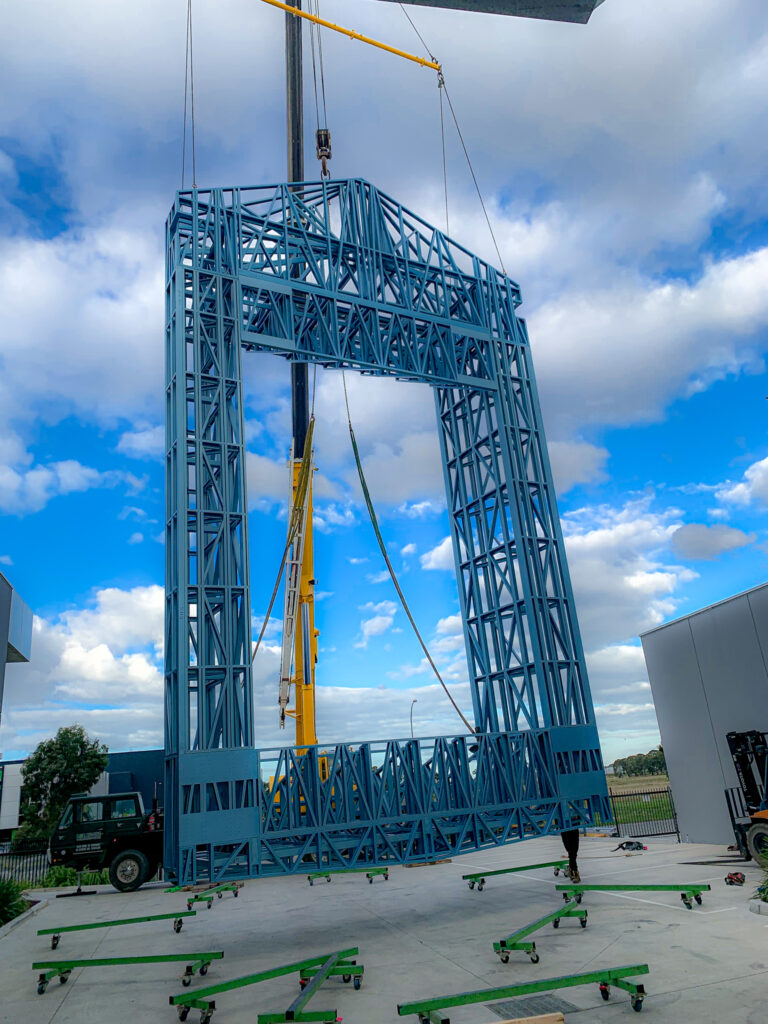
How do you manage client expectations and ensure we deliver on time?
Ensuring our clients time frames are met is extremely important to us as a company. We work closely with external crane truck services where required whilst also utilising our own crane truck and driver, this helps us achieve customers delivery targets to the best of our ability.
Alvin – Production Manager
Since the arrival of the deep c machine (Bertha) how has this helped with production of flooring systems?
Since the arrival of our Hyperspan machine, production of floor members is a lot quicker with less man power required. Bertha produces approximately 4 townhouses worth of floor systems a day with 2 people, in comparison to 2 townhouses a day with 4 people. That said, productivity has increase dramatically since.
Alvin – Production Manager
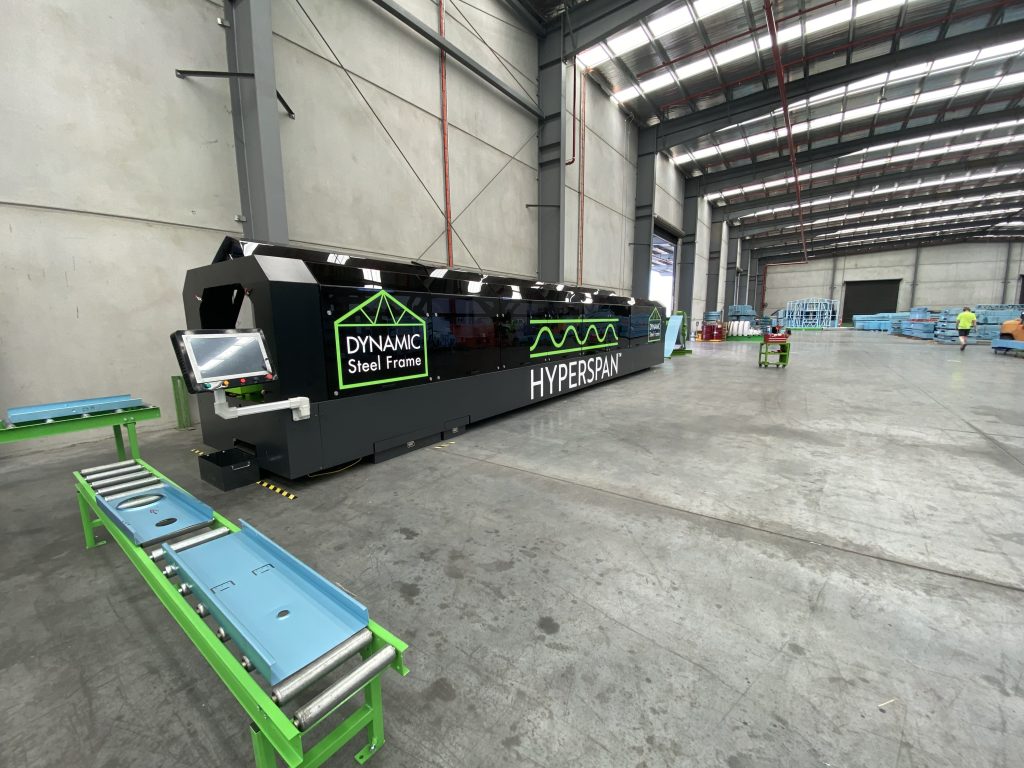
How has the implementation of mission control been a game changer for production?
Implementing Mission Control into Dynamic Steel Frame has dramatically impacted production. As a rapidly growing business, Mission Control empowers us to effectively manage projects, foster transparency, and accommodate future growth. It’s integration with Salesforce provides a unified customer view, cross-departmental transparency, and scalability for our expanding operations. Making the change to Mission Control has caused greater customer satisfaction and has been immensely helpful for all staff when scheduling deliveries and staff requirements.
Tasha – Business Administration Manager
In ensuring frames are good to go prior to rolling, what processes are implemented?
Before the frames are sent into production for rolling, we take a look through the 3D generated model and frame drawings to ensure there are no clashing members and the dimensions specified on the detailed plans are actually achievable. We also must ensure that the frames will be safe for transport before being produced. If the frames don’t work, a quick query with the detailer of that project will help us come up with an alternative solution. By double checking everything prior to rolling this reduces the likely hood of variations due to detailer errors and slowing down production times.
Alvin – Production Manager
If an issue comes up during the production of frames, how do you go about rectifying this?
The main issues that arise is the machine breaking down, putting a halt on production. Fortunately this is addressed almost immediately and fixed by the team if possible. Depending on the urgency of the job that was rolling through, we may move production of those frames onto another machine.
Alvin – Production Manager
What does the future of production at Dynamic Steel Frame look like to you?
As we figure out the nuances behind production of flooring joists on our newest hyperspan machine, we can see most of the floor joist production going to that machine. This allows us to produce more product in a shorter time frame.
And with construction timber prices to remain high all the way to July 2024, according to Lumber futures contracts, steel is only getting more price competitive against timber, as steel prices seem to be holding steady at the moment.
With the new machine taking up the brunt of the production load of flooring members, we can concentrate on more wall and truss jobs. It is quite exciting as there is a massive shortage of housing at the moment, and knowing that steel will inevitably come to occupy a larger part of this market means DSF will be getting quite busy, very soon.
Alvin – Production Manager
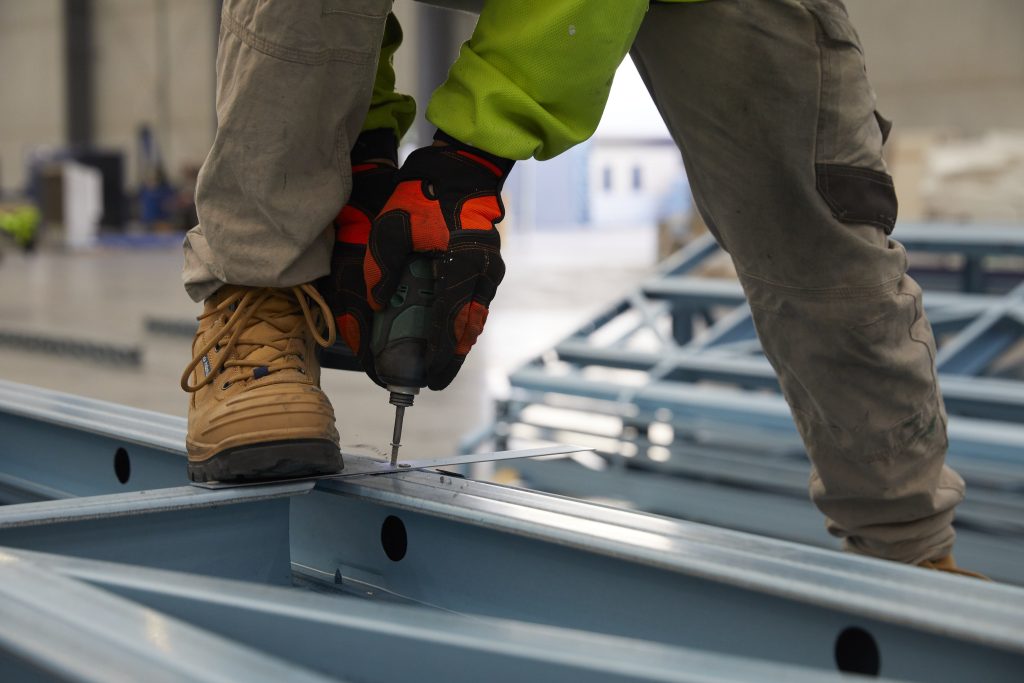
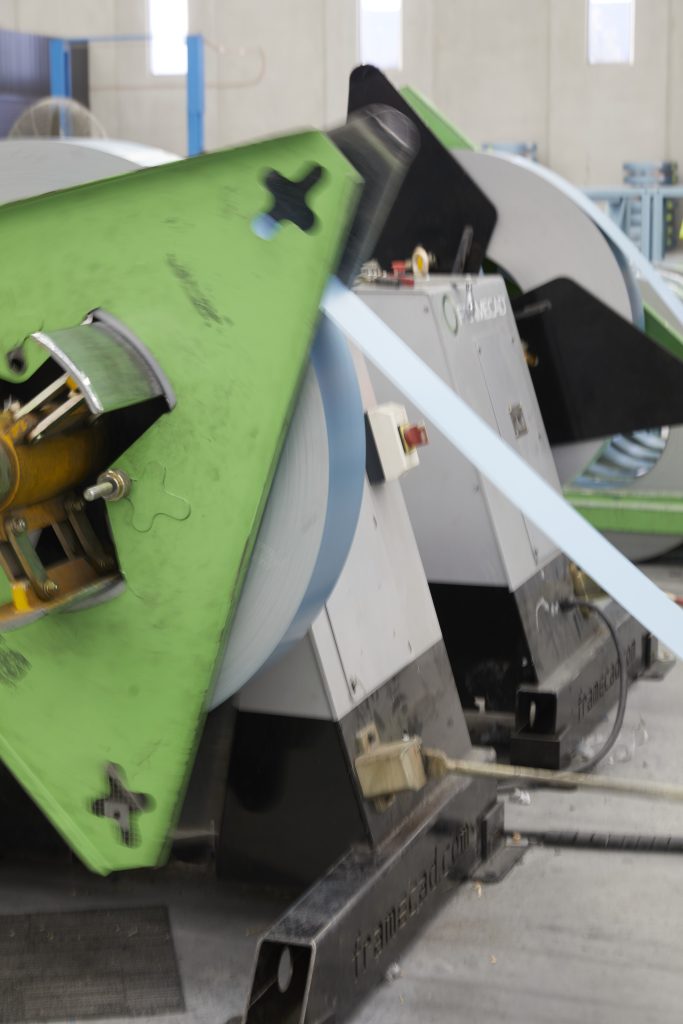
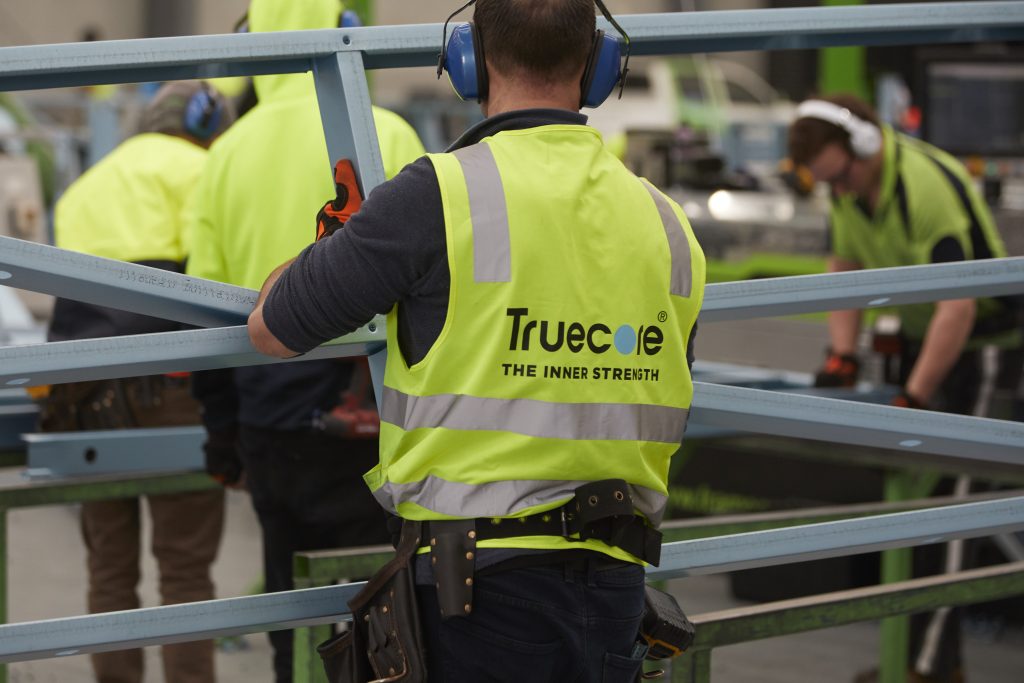
If you are looking to use light gauge steel framing made from TRUECORE® steel for your next project, contact the team at Dynamic Steel Frame to get your project underway.
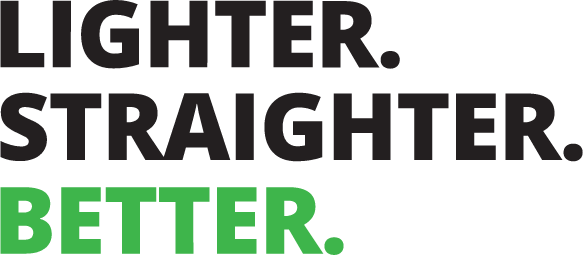
Phone: 03 9701 7342
Email: sales@dynamicsteelframe.com.au